Case Study: Onshore Installation
Emulsion Monitoring in Production Separator
The ROCSOLE LiquiDetect 2.0 was installed in a production trap vessel to address emulsion issues, and after initial success, a longer profiler was added to monitor produced water quality, enhancing emulsion monitoring in production separators.
This technology, featuring a 64-electrode sensor, has improved liquid management and is set to be implemented in additional vessels to enhance facility performance.
ROCSOLE LiquiDetect 2.0 Profiler enhances operational efficiency by providing real-time monitoring and control of gas, oil, and water levels, even in high-pressure environments. Its advanced technology enables proactive maintenance and optimized liquid management practices, ensuring smooth operation and minimizing downtime.
The installation of the LiquiDetect 2.0 marks a significant advancement in liquid management practices.
The project started as a pilot in one of the High-Pressure Production Trap (HPPT) vessels within one of the oil trains in the field. The customer was experiencing issues with increasing emulsion levels within the oil trains. ROCSOLE LiquiDetect 2.0 was installed in July 2023 and connected to the Distributed Control System (DCS) in September. After the initial setup, the client requested the installation of a longer profiler to enable monitoring of the produced water quality as well.
Challenge
The maturity of the field has increased the volume of emulsions entering the separator, which impacts the quality of the crude oil to be exported and the produced water to be disposed of.
To maintain the necessary export/discharge quality, the customer has increased the usage of demulsifiers and water treatment chemicals.
Due to the design of the downstream produced water facilities, the customer needs to minimize the oil content in water from the vessel. Therefore, they need to monitor the full operating range of the vessel.
Solution
Installation of the ROCSOLE LiquiDetect 2.0 enabled accurate monitoring and measurement of the emulsion layer and provided information on its dispersion within the separator.
Extending the profiler to include the full produced water region prevents “high oil in water” excursions.
The next phase of the project is the implementation in the remaining High Pressure Production Trap (HPPT) vessels to enhance the overall performance of the facility.
Meet the team to tackle the challenge
All success is based on great teamwork and in this case we’d like to thank our client's team for the great cooperation. Please meet the Rocsole team involved:
Enhanced Liquid Management: Proven Results with LiquiDetect 2.0
The implemented system features an advanced technology with a 64-electrode sensor, certified for reliability in hazardous environments. Operating within specified pressure and temperature ranges, the system offers comprehensive liquid management capabilities. The successful deployment of this solution marks a significant advancement in liquid management practices within the industry.
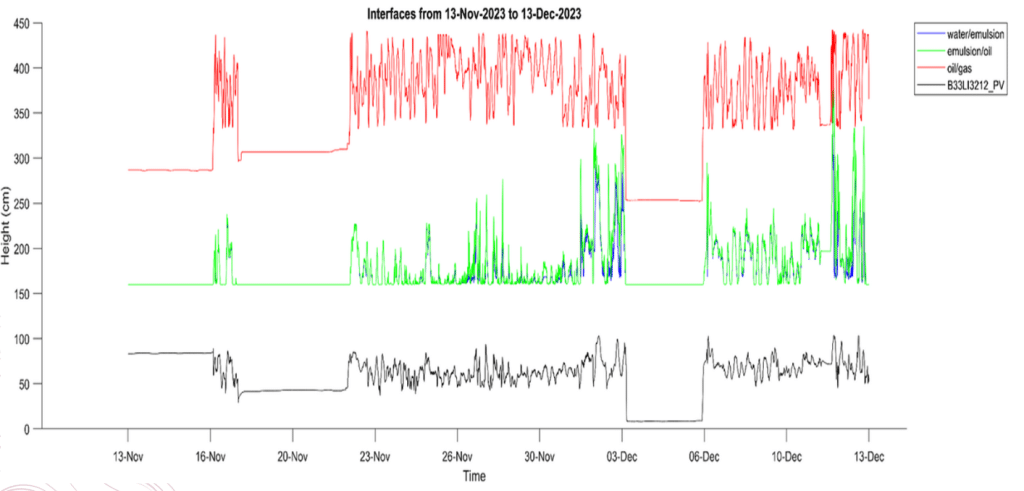
The Details in Overview
System Design:
- Operating Pressure: 3.45 bar
- Design Pressure: 6.9 bar
- Operating Temperature: from +35 °C (95 °F) to +47 °C (115 °F)
- Design Temperature: -2 °C (28 °F) to 74 °C (165 °F)
- 1 x 64 Electrode sensor
- User Interface webroc 1.0
Delivery Content:
The installed package contained the Rocsole liquid management system LiquiDetect 2.0
- 64 electrodes of measurement area 2880 mm
- IECEx certified
- Sensor material Alloy EN 2.4602 (C22)
- Electronic cabinet L size, material - Aluminium Epoxy coated
- Vessel top installation via existing nozzle
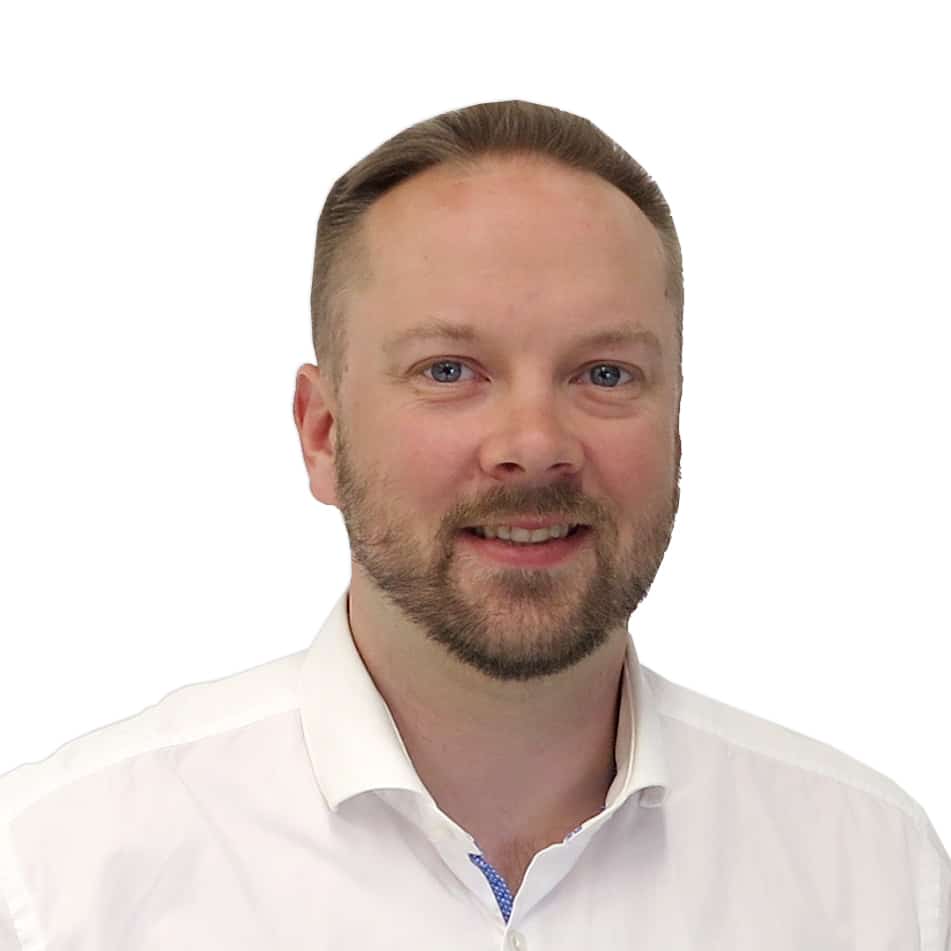
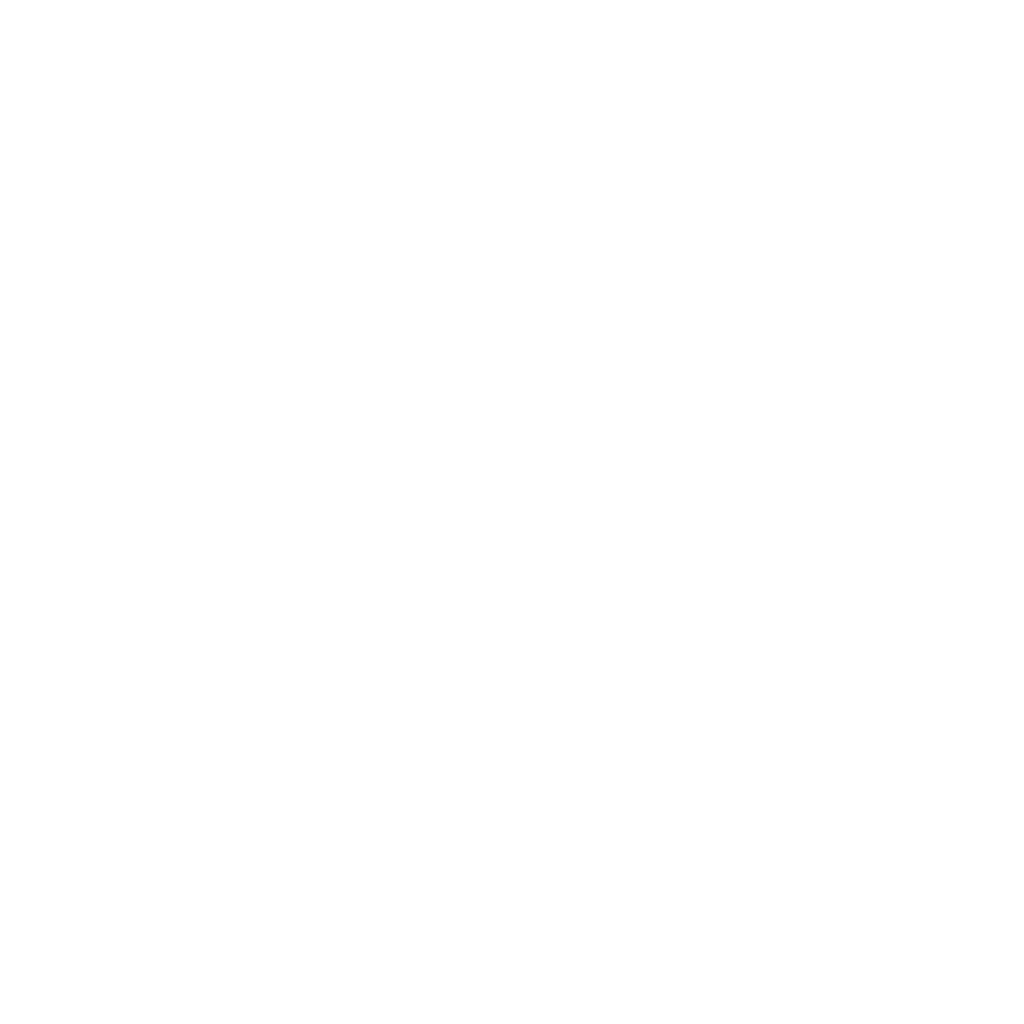