Case Study: Onshore Liquid Management
Optimizing Onshore Liquid Management with Real-Time Monitoring and Control
LiquiDetect 2.0 system was integrated into a customer’s Digital Control System for real-time monitoring and control of onshore fluid management, addressing challenges like unreliable instrumentation and wax formation.
The system’s rapid response rate and adaptability proved essential in managing highly variable operations, allowing for maximized production control.
Continuous support and software updates ensured the system’s efficiency in adapting to process demands, leading to the customer’s decision to replace existing equipment with the LiquiDetect 2.0.
LiquiDetect 2.0 ensures efficient liquid management in challenging onshore environments.
The customer operates in areas with tight (low porosity) onshore locations, employing advanced drilling techniques including horizontal drilling and hydraulic fracking. The extracted oil is generally light, while the natural gas production volume varies. However, during flowback and production numerous challenges arise due to the reliability and responsiveness of the instrumentation. Reliable monitoring of gas, oil, and water levels, as well as managing oil/water mixing, are critical. Additionally, variations in ambient conditions can lead to the formation of wax, presenting further operational challenges.
Challenge
The existing installed instrumentation fails to accurately measure and report the process data, specifically during chaotic situations, e.g., pipeline pigging.
The instrumentation needs to be fast and precise to capture the changes that occur and allow the customer to optimize the process and predict future issues.
The system also needs to be flexible to be fine-tuned based on the results obtained.
Solution
The LiquiDetect 2.0 was integrated into the Digital Control System (DCS), allowing real-time monitoring and control of water and oil levels.
Remote data interpretation and support enable the data and settings to be reviewed and optimized based on the data collected.
The conductivity profiles generated offer the customer valuable insights into the process, enhancing control and decision-making.
Based on the feedback and performance, the customer intends to replace existing equipment and utilize a support contract to improve data interpretation.
Meet the team to tackle the challenge
All success is based on great teamwork and in this case we’d like to thank our client's team for the great cooperation. Please meet the Rocsole team involved:
LiquiDetect 2.0 system's rapid response rate and adaptability proved essential in managing highly variable operations, allowing for maximized production control.
The ROCSOLE sensor is capable of measuring multiple material interface levels simultaneously. Interface position trends can be viewed in the ROCSOLE Webroc GUI and the system can also be integrated into Distributed Control System (DCS) and Supervisory Control and Data Acquisition (SCADA) environments.
Results
The ROCSOLE LiquiDetect 2.0 system generates a large volume of data from a process. When the operations are highly variable, the response rate and update time are essential for the users to control and maximize production. The data collection and reporting system needs to be flexible and adaptable to accommodate changes in production. Through continuous support, software updates, and tuning the computations, the LiquiDetect 2.0 easily adapts and responds to process demands.
The Details in Overview
System Design:
- Operating Pressure 1100 kPag (11 bar)
- Design Pressure 5000 kPag (50 bar)
- System Operating Temperature under +45 °C
- Design Temperature -29 °C to 50 °C
- 1 x 64 Electrode sensor
- User Interface webroc 1.0
Delivery Content:
The installed package contained the Rocsole liquid management system LiquiDetect 2.0
- 64 electrodes of measurement area 2880 mm
- CSA certified
- Sensor material EN 1.4410
- Electronic Cabinet material Aluminium Epoxy Coated
- Vessel top installation via existing nozzle
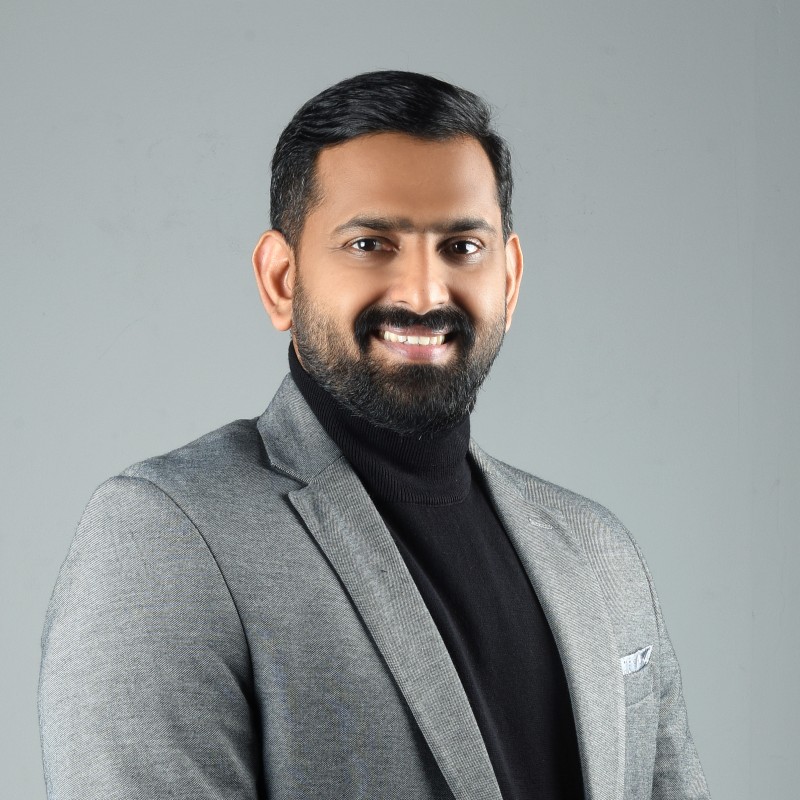
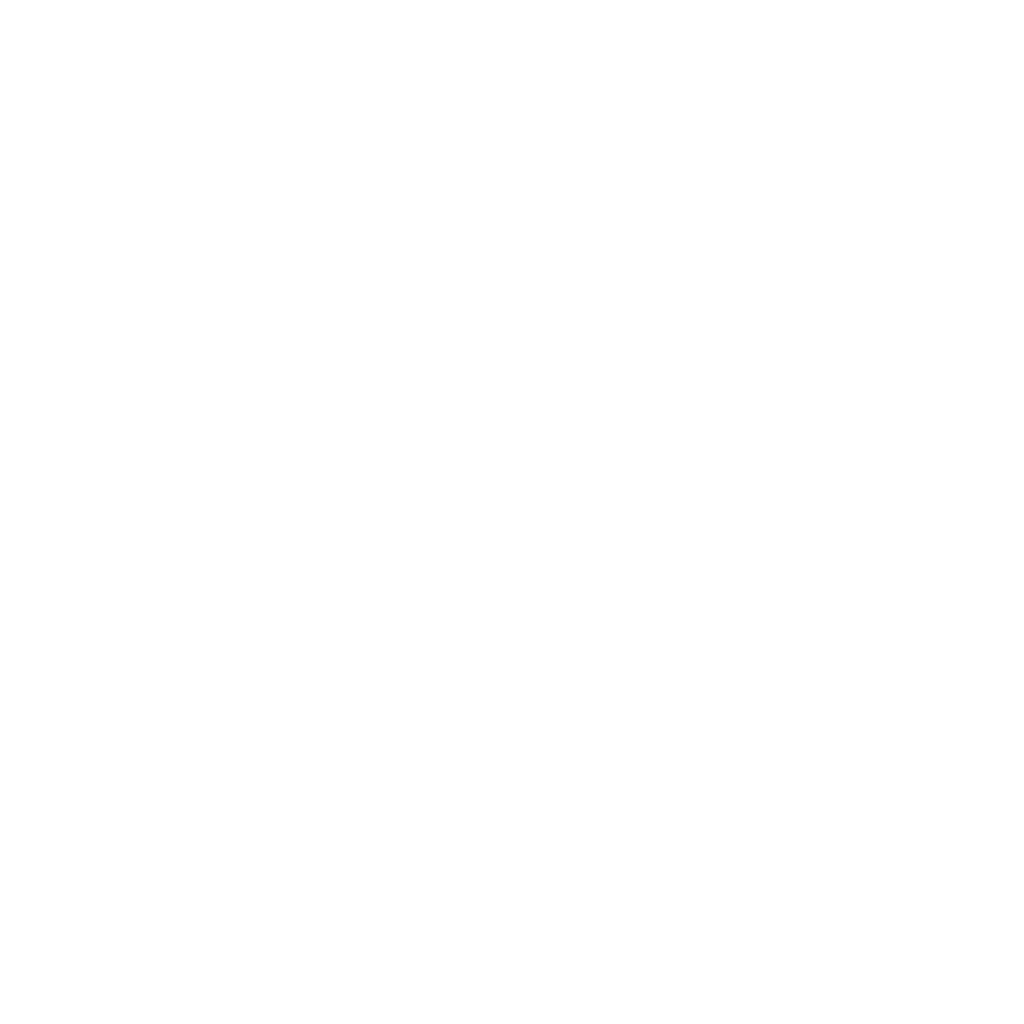