CASE STUDIES
Understanding Oil-Water Separation and Emulsions in Mature Fields
The client required a reliable profiling device which could help them to understand the separation process before, during and after EOR treatments. Ideally the data could identify bottlenecks in the existing crude dehydration equipment; consequently the client could maximise their oil production from the fields. Detailed insights of oil-water separation and dispersion band depth were provided by Rocsole LiquiDetect 2.0 system.
Some facts for context
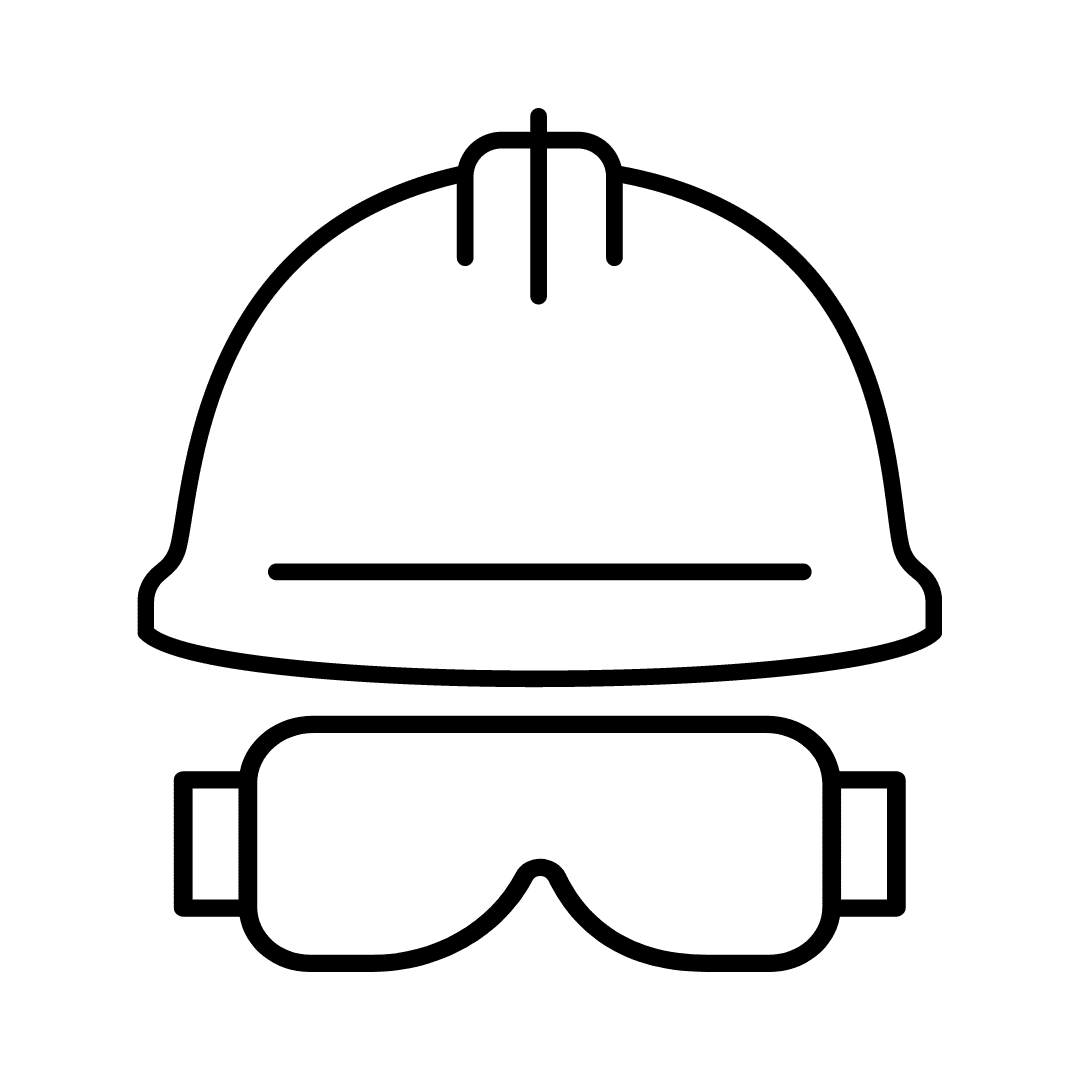
THE CLIENT
The client is a leading oil & gas exploration and production company in The Middle East Region.
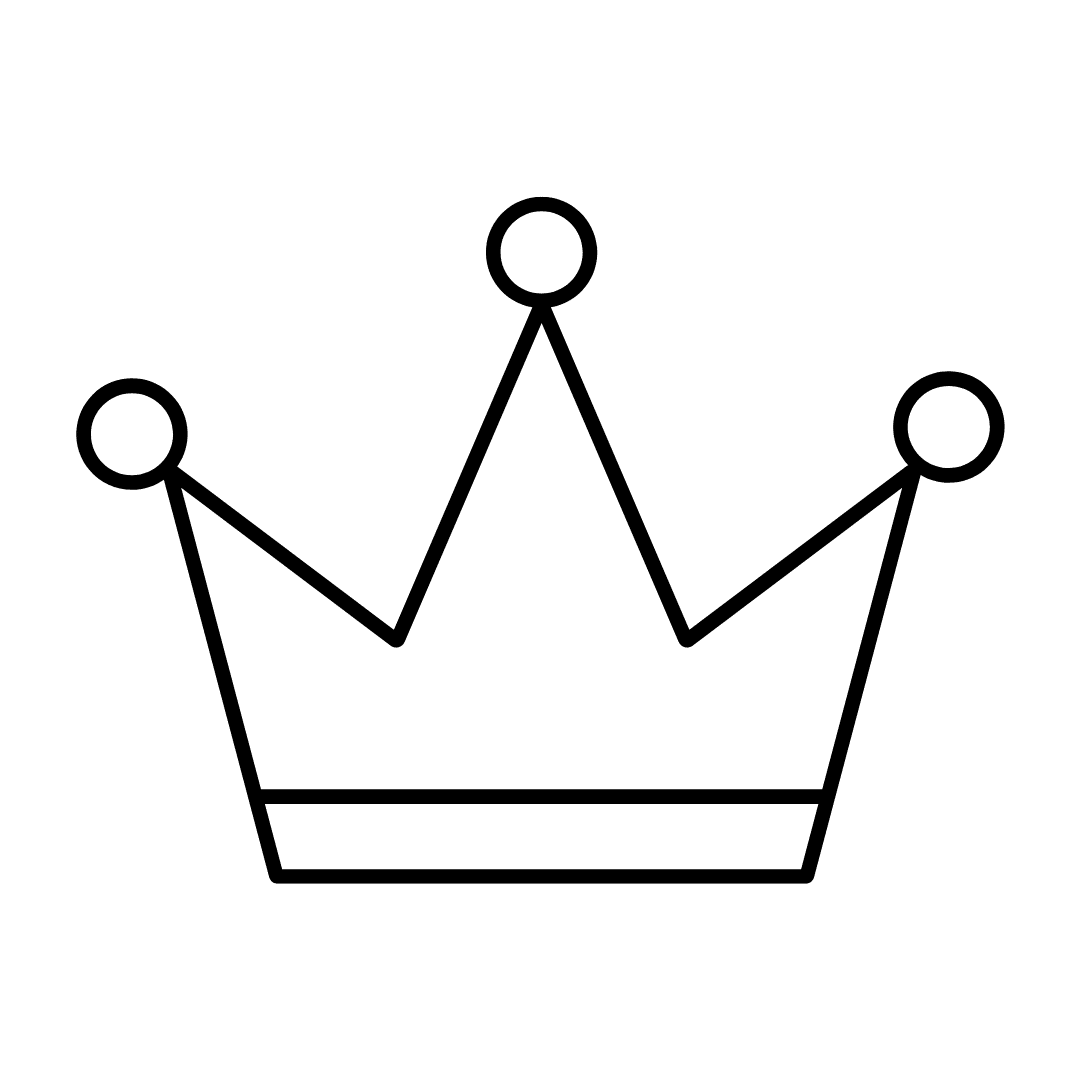
STAKEHOLDERS
The client is a governmental owned company, and partly owned by an Major Independent Oil Company.
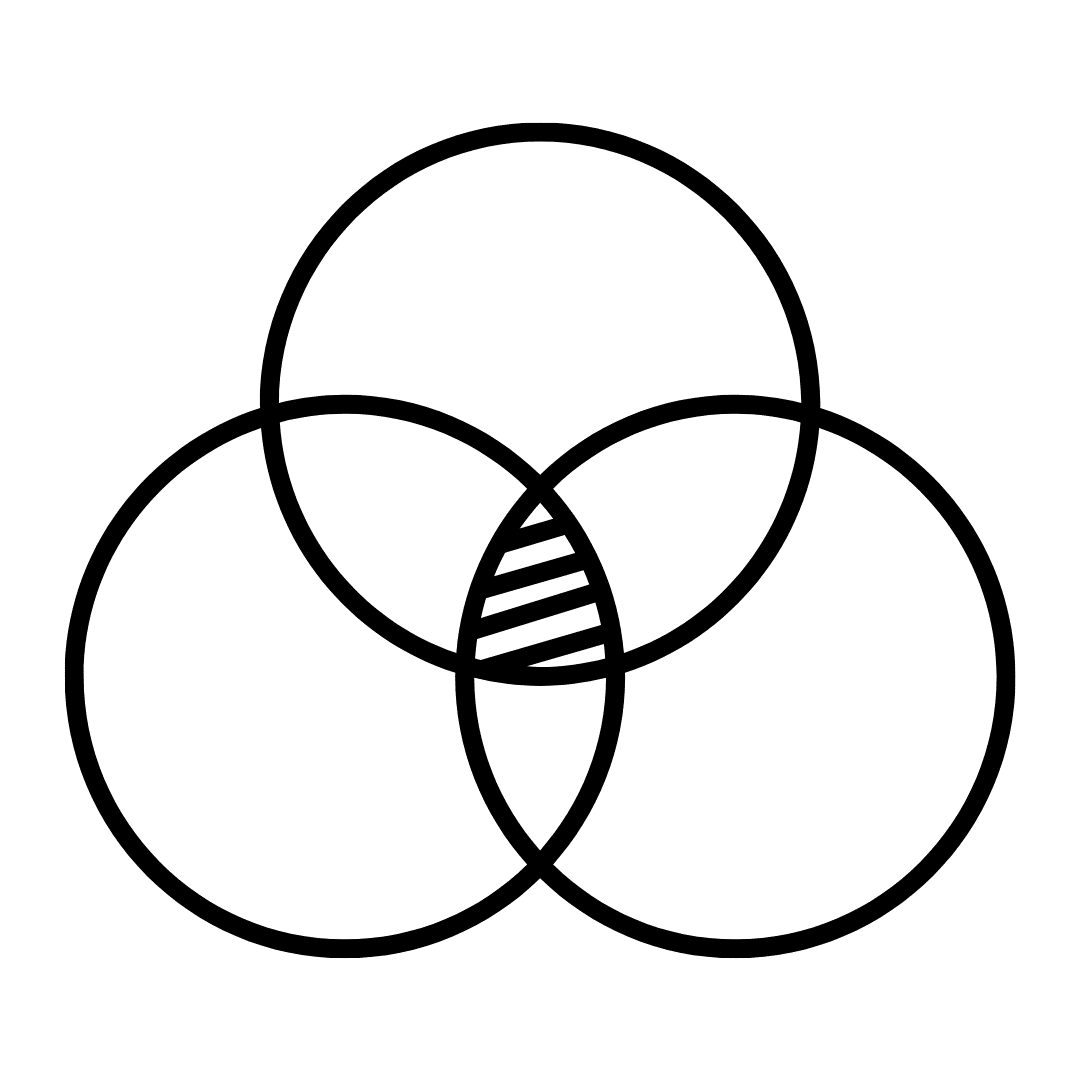
BASIS OF DESIGN
The field is using Polymer Flooding for enhanced oil recovery (EOR), this will maintain and potentially increase the current production of crude oil. The field is classified as heavy crude oil with one of the highest viscosity in the region.
With the client's target to achieve full field application of Enhanced Oil Recovery (EOR) solution.
The Challenge
The assessment of the overall impact of back-producing EOR fluids on the oil-water separation could not be quantified, which prevented full field implementation.
The existing Level Control Device (DP) installed was unable to differentiate between the oil/emulsion/water interfaces during the first flow back from the wells.
The density difference between the oil and emulsion layers was very small, which meant accurate identification and control was difficult.
The Need
Understanding the impact of the EOR Chemicals on the separation process is required so that the customer can upscale the technology to full field implementation also to identify any bottlenecks within the existing production system which might limit production.
Overall there is a need to keep oil-in-water value within environmental limits and BS&W within the agreed range.
A 24/7 Emulsion Monitoring and Management Solution
After a review of the technologies available, Rocsole LiquiDetect system was selected. In this application 3-metre sensor was installed with an active measurement area of 2 metres.
The test separator has inner diameter of 2800 mm. Typical measurement area for 64 electrodes is 1440 mm or 2880 mm. And Rocsole suggested and offered LiquiDetect 2.0 with 1968 mm (30,75 mm x 64 electrodes) so that the whole emulsions separation phase would be fully covered.
Rocsole LiquiDetect 2.0 was installed into the customer's Test Separator in June 2020.
Some interesting details about oil-water separation
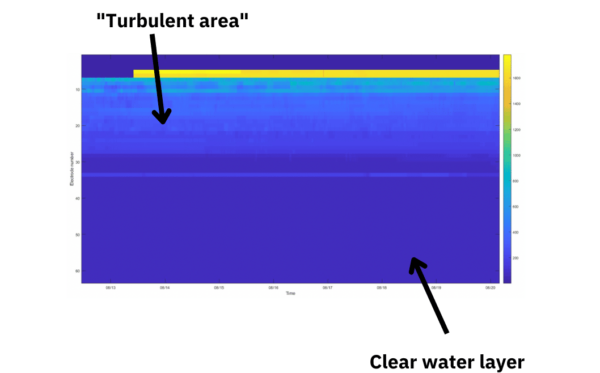
The initial data showed a significant "turbulent zone" within the vessel, which appeared to be a mixture of foam and emulsion.
The testing and data collection continued for approximately 12 months and was clearly able to identify the oil/gas, oil/emulsion and water interfaces during the entire period.
The "turbulent area" when reviewed with the design and the production data, showed that a significantly large volume of gas entered the vessel and this gas volume overloaded the inlet device, of forcing the gas down into the liquids causing turbulence/foam. The foam generated was unstable and broke down quickly.
Get Data to help understanding of your operation
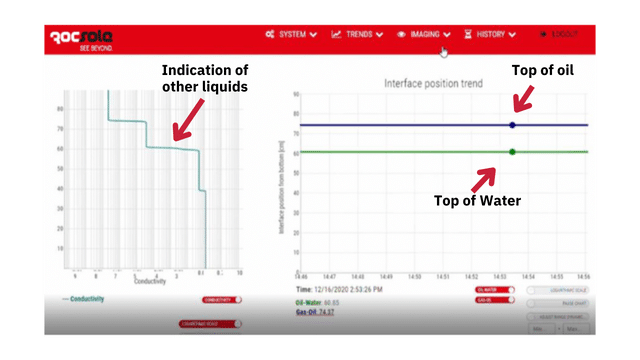
Operations Challenge
The use of EOR Reservoir Treatments can cause changes in the physical properties in the oil and emulsions, in particular the fluids density. Consequently, it can interfere with accurate identification of the oil/emulsion interface and the emulsion/water interface. Lack of accuracy in the interfaces can cause issues with excess water being exported with the oil and higher than allowed oil in water values, it can also increase the required retention time and reduce throughput.
Solutions Discovered
The analysis of the dispersion band height was supplied to the customer and then combined with the production data, well configurations weekly system data. This gave the customer more understanding of the different emulsions present in their operation. It also highlighted an issue with the operation of the chemical treatment equipment which was not detected by the operators.
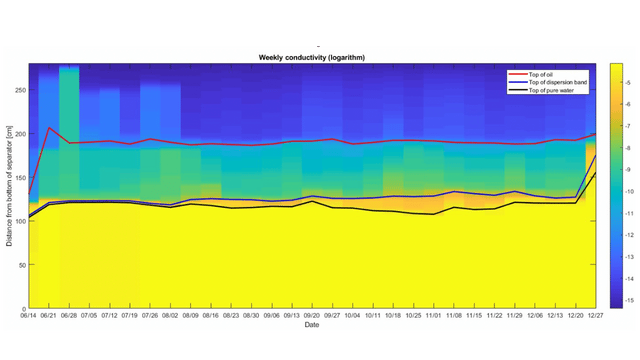
All covered?
Yes, indeed.
Data analysis
Apart from interface levels, Rocsole provides a data analysis service upon request to give further insights and better understanding. In this case, the customer could make reactive decisions on their EOR treatments and plans.
Reduced occupation hazard
LiquiDetect 2.0 system has an HSSE benefit in comparison with the other main alternative, this was recognised and highlighted by the Client.
Robust performance despite fouling
During the trial, it was acknowledged by the customer that there was no observable impact due to fouling on the Rocsole LiquiDetect 2.0, system, even in the presence of the heavy waxy oil. A full inspection will be conducted when after the device is retrived from the vessel.
Financial benefits
The client claimed to have a significant immediate CAPEX benefit compared to other alternatives. In addition, the improved process monitoring from Rocsole LiquiDetect 2.0 meant that the customer could save expenses in EOR treatment and increase their overall performance.
Oil-Water separation insights are now available with Rocsole SeeBeyond
The Rocsole LiquiDetect uses electrical tomography technology to identify the interfaces within the vessel under normal operation and after the EOR treatment return.
Different production fluids were analysed and the customer gained an understanding of the changes that occurred due to EOR Treatment and this knowledge will be essential when the full field implementation of EOR is deployed.
With the Rocsole LiquiDetect 2.0 system, the Rocsole team again was able to help another client to “See Beyond”, fulfilling their commitment to:
With the Rocsole LiquiDetect 2.0 system, the Rocsole team again was able to help another client to “See Beyond”, fulfilling their commitment to:
- understanding separation impact under EOR treatment
- identify bottlenecks & ability to upscale production
- ensuring HSSE safety
The details
System design:
Operating Pressure under 65 psi (under 4.5 bar)
Design Pressure 1440 psi (100 bar)
Operating Temperature 104-122 °F (40-50 °C)
Design Temperature 194 °F (90 °C)
1 x 64 Electrode G3 sensor (3121 mm in total length)
User Interface Webroc 1.0
Delivery content:
The installed package contained the Rocsole
liquid management system LiquiDetect 2.0 consisting of:
64 electrodes (G3) of measurement area
IECEx certified
Sensor material 1.4404 – 316L, coated for stainless steel parts
Electronic cabinet material - Aluminium Epoxy coated
Vessel top installation via existing nozzle
Learn more about LiquiDetect.